Tout savoir sur les presses électriques
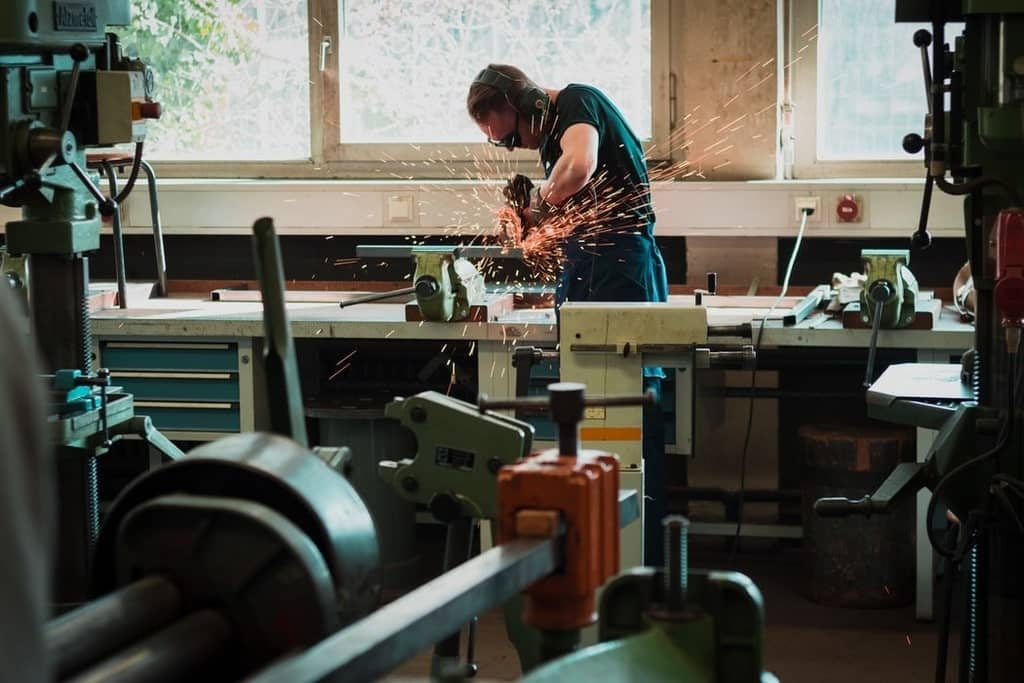
La presse est une machine de formage des métaux. Elle est conçue pour former ou couper le métal en appliquant une force ou une pression mécanique. À l’aide d’une presse, vous pouvez former le métal comme vous le souhaitez sans enlèvement de copeaux. Les presses sont exclusivement destinées aux travaux de production en série. Elles constituent le moyen le plus rapide et le plus efficace de transformer n’importe quelle tôle en produit fini.
Les origines de la presse à machines
Avant l’invention de la presse mécanique, les ouvriers devaient marteler le métal à la main pour en modifier la forme. Non seulement cette opération était physiquement pénible, mais elle était également inefficace lorsqu’elle était effectuée sur des métaux durs et résistants. Vers le milieu des années 1800, cependant, le marteau à vapeur a été développé.
Également connu sous le nom de marteau à chute, le marteau à vapeur était essentiellement une première version de la presse mécanique moderne. La seule différence est que le marteau à vapeur était actionné par la vapeur, alors que la plupart des presses modernes sont actionnées par l’hydraulique.
Qu’est-ce qu’une presse électrique ?
Introduites en 1984 au Japon, les machines de presse par injection entièrement électriques sont relativement nouvelles sur le marché. Cependant, après une adoption rapide, elles représentent maintenant plus de la moitié de toutes les machines vendues. Ces machines sont alimentées par des servomoteurs à grande vitesse à commande numérique plutôt que par l’hydraulique.
Ce qui permet un fonctionnement plus rapide, répétable, précis et économe en énergie. Le fonctionnement des machines électriques est très prévisible, de sorte qu’une fois qu’un processus d’injection souhaitable a été atteint, il peut être reproduit de manière très régulière. Il est alors possible d’obtenir des pièces de meilleures qualités.
Une fois qu’un travail a été programmé dans une machine électrique, ses commandes numériques lui permettent de fonctionner pratiquement sans surveillance, ce qui réduit les coûts de main-d’œuvre et augmente les profits.
Comme il ne présente aucun risque de contamination par l’huile, la presse à injecter électrique est bien adaptée aux applications en salle blanche. En raison de sa grande précision, ce procédé est également idéal pour les pièces de petite et moyenne taille et les produits médicaux tels que les boîtes de Pétri et les seringues. Parmi les autres avantages, l’on peut citer :
- la précision et répétitivité élevée avec des taux de rebut réduits ;
- un procédé plus propre qui ne laisse jamais de traces ;
- la réduction des temps d’arrêt généralement associés à l’hydraulique ;
- une économie d’énergie de 30 à 70 % ;
- un fonctionnement plus silencieux, bruit du moteur réduit à moins de 70 dB ;
- des vitesses d’injection plus rapides jusqu’à 800 mm/sec ;
- un mouvement de pince plus rapide ;
- un temps de démarrage plus court et des cycles jusqu’à 20 % plus rapides ;
- un coût unitaire plus faible avec moins de déchets matériels ;
- ne nécessite aucun consommable, tel que de l’huile qui devrait être remplacée ou nettoyée ;
- la réduction des besoins en énergie grâce à des coûts d’exploitation nettement inférieurs.
Bien que les machines électriques soient plus rapides, plus propres et plus efficaces sur le plan énergétique, elles ne sont pas en mesure d’atteindre les forces de serrage produites par les machines hydrauliques et ont également un coût initial plus élevé. Il s’agit de machines à serrage à genouillère actionnées par des vis à billes, qui sont toutes deux des pièces d’usure.
Elles peuvent être coûteuses à remplacer ou difficiles à trouver sur le marché de l’occasion. Malgré leur grande précision, les machines électriques peuvent être moins indulgentes que les presses hydrauliques en raison de leur grande précision de positionnement.
Comment fonctionnent les presses à machines ?
Bien que la mécanique exacte varie selon le type de presse, la plupart des presses fonctionnent en pressant une plaque ou une matrice sur ou contre une pièce. Elles sont commandées par un ou plusieurs ouvriers appelés régleurs d’outils qui positionnent la pièce et contrôlent la presse.
Une fois que la pièce est positionnée sous la plaque ou la matrice de la presse, le régleur d’outils active la presse. En utilisant la pression hydraulique, la presse pousse la plaque ou la matrice contre la surface de la pièce, ce qui provoque la déformation de la forme de la pièce.
La pression générée par les presses mécaniques
Les presses mécaniques dépendent de la haute pression pour réaliser les applications prévues. À l’exception des presses plus légères, telles que les presses à arbre, la plupart des presses utilisent environ 1 à 30 tonnes de pression. Elles sont donc capables de déformer la plupart des matériaux.
Le bronze, le cuivre, l’aluminium, le fer, l’acier et les matériaux composites par exemple. La pression élevée d’une machine de presse écrase même les métaux les plus durs, ce qui permet aux entreprises manufacturières de déformer les pièces métalliques pour leur donner la forme souhaitée.
Comment bien utiliser une presse électrique ?
Comme pour toute machine lourde, une formation est nécessaire pour utiliser une machine de presse. L’opérateur est confronté à de nombreux risques dans le cadre de son travail. Ces machines utilisent des pressions et des forces incroyablement élevées pour déformer le métal selon les besoins. Ces pressions peuvent causer des blessures extrêmes, voire la mort d’un opérateur.
Avec les presses hydrauliques ou pneumatiques, les liquides ou les gaz sont contenus sous une chaleur ou une pression élevée. Il existe un risque de blessure si des parties de la presse tombent en panne et pulvérisent des fluides sur l’opérateur. Il peut y avoir d’autres risques selon les matériaux, les métaux et les fluides utilisés pour créer les pièces. Dans la plupart des cas, les industries sont bien informées.
Elles dispensent également une formation générale en matière de sécurité pour faire face à tous ces risques potentiels. Une formation opérationnelle est également nécessaire. De nombreuses presses modernes sont commandées numériquement, ce qui permet à l’opérateur de prendre une certaine distance par rapport au processus. Cependant, la saisie manuelle est souvent nécessaire.
Dans la plupart des cas, cela implique le chargement ou le déchargement des matrices requises qui forment une pièce particulière ou des ajustements manuels nécessaires pour s’assurer qu’elles s’alignent correctement au début du processus.
La saisie manuelle peut également impliquer le chargement de la matière première métal ou le déchargement du produit fini, bien que ce processus soit souvent automatisé. Dans la plupart des usines modernes, cet équipement est automatisé et les opérateurs n’ont besoin d’intervenir que pour le dépannage.
En savoir plus sur les presses électriques
Découvrez-nous derniers articles :
- 3 astuces efficaces pour économiser de l’énergieL’une des premières raisons pour lesquelles de nombreuses personnes se préoccupent de leur consommation d’énergie est la flambée des coûts de l’électricité. Or, il est important de s’en soucier également pour la survie de
- Comment lire efficacement une plaque signalétiqueL’essence de la plaque signalétique dans le monde des moteurs électriques La plaque signalétique d’un moteur électrique est bien plus qu’une simple étiquette collée sur le côté d’une machine. Elle est le reflet des
- Comment fonctionne un moteur électrique ?Le moteur électrique est l’une des inventions les plus importantes de l’histoire de l’ingénierie électrique. Il est utilisé dans une variété d’applications industrielles, des voitures électriques aux machines industrielles en passant par les appareils
- Quels sont les avantages et les inconvénients d’un moteur électrique ?Les conditions climatiques récentes ont poussé à la création des moteurs électriques qui sont de nos jours la meilleure option pour diminuer l’émission excessive du carbone. Les avantages que possède un moteur électrique ne
- Presse électrique : les utilisationsNotre ère est la grande époque où la transformation mécanique connaît un essor phénoménal. Parmi les machines les plus utilisées, il y a la presse électrique. Il est question d’une machine de manipulation et